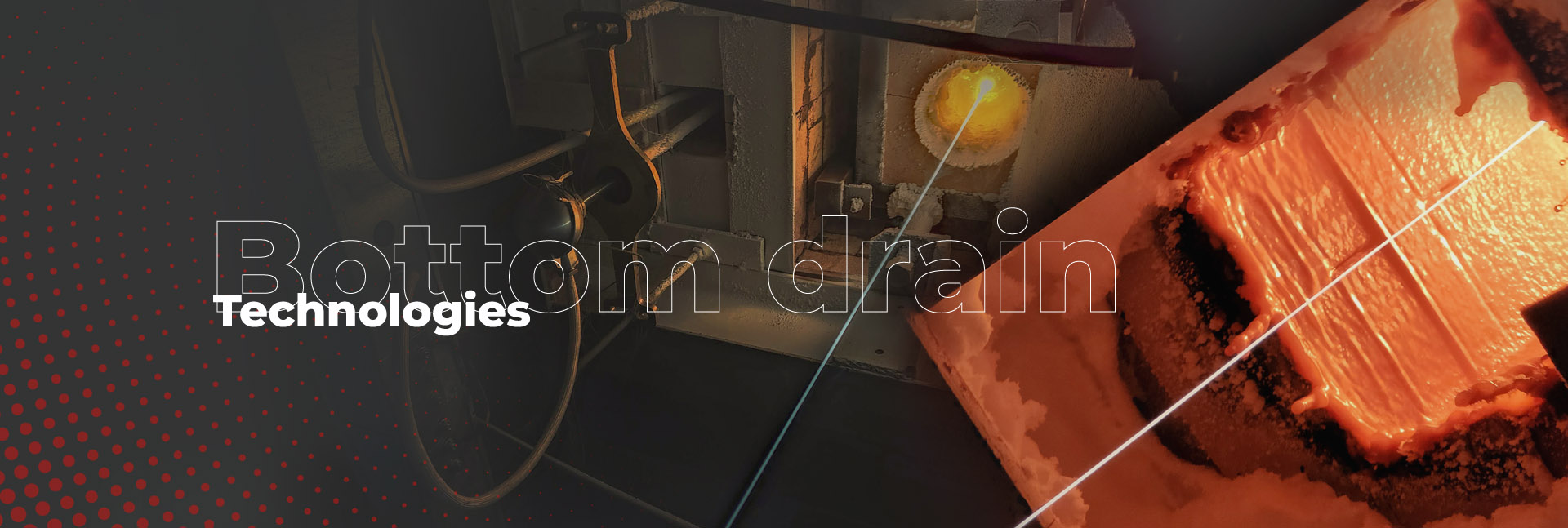
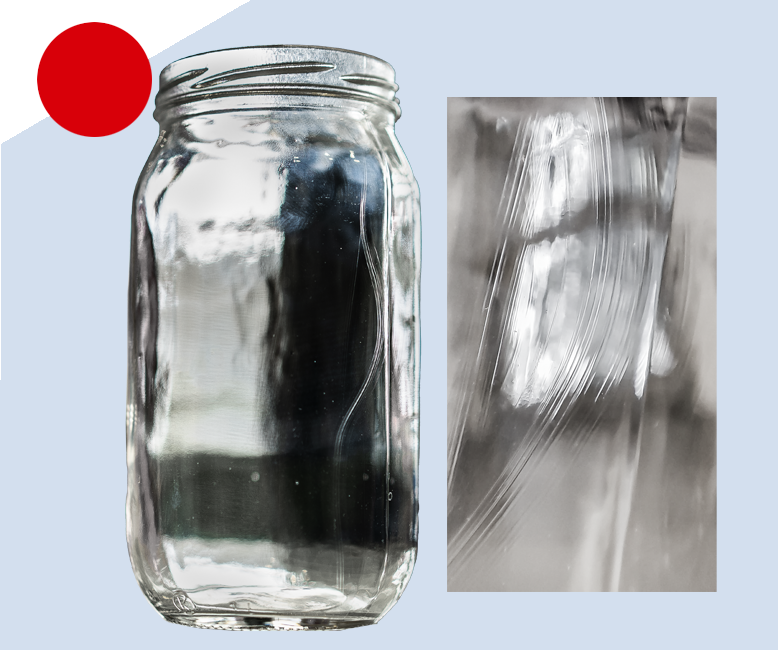

Glass Service design
Bottom drain
technologies
Zircon cords, also known as “cat scratches”, pose a growing concern for glass manufacturers worldwide. In the glass industry, especially for products like tableware, pharmaceutical tubes, molded borosilicate glass, and TFT glass for screens, the absence of cords is a fundamental and critical requirement. Although there’s no evidence suggesting cords affect the physical properties of containers, the glass container market is increasingly emphasizing cord-free glass. Zircon cords are inherent to the glass manufacturing process, stemming from the presence of ZrO2 in furnace and forehearth construction materials. Physical and chemical erosion leads to the formation of zircon-rich glass, which tends to separate from the base glass, resulting in the well-known zircon cords.
Glass Service has designed and developed an effective Bottom Drain system that ensures maximum removal of zircon-enriched glass, guaranteeing compliance with the most stringent requirements for cord-free glass either independently or in conjunction with stirrers.
Bottom drain technology
uses the following main features:
- Refractory design bottom Zirconium trap special block
- Pt/Rd plate with calibrate hole direct heated DHT (Direct Heating Technology) by electrical current
- Air cooling Molybdenum electrode
- Electric power circuit including thyristor unit and power transformer
- Air cooling ring (fans) to prevent glass leak
- Platinum immersed thermocouple for glass temperature reading
The trap block is specially designed to ensure effective separation between high-quality glass and zircon-enriched glass to be drained out. Constructed from fused cast AZS material, the block features a shaped and calibrated drain hole at the bottom
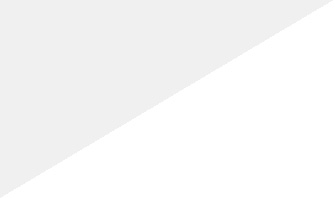
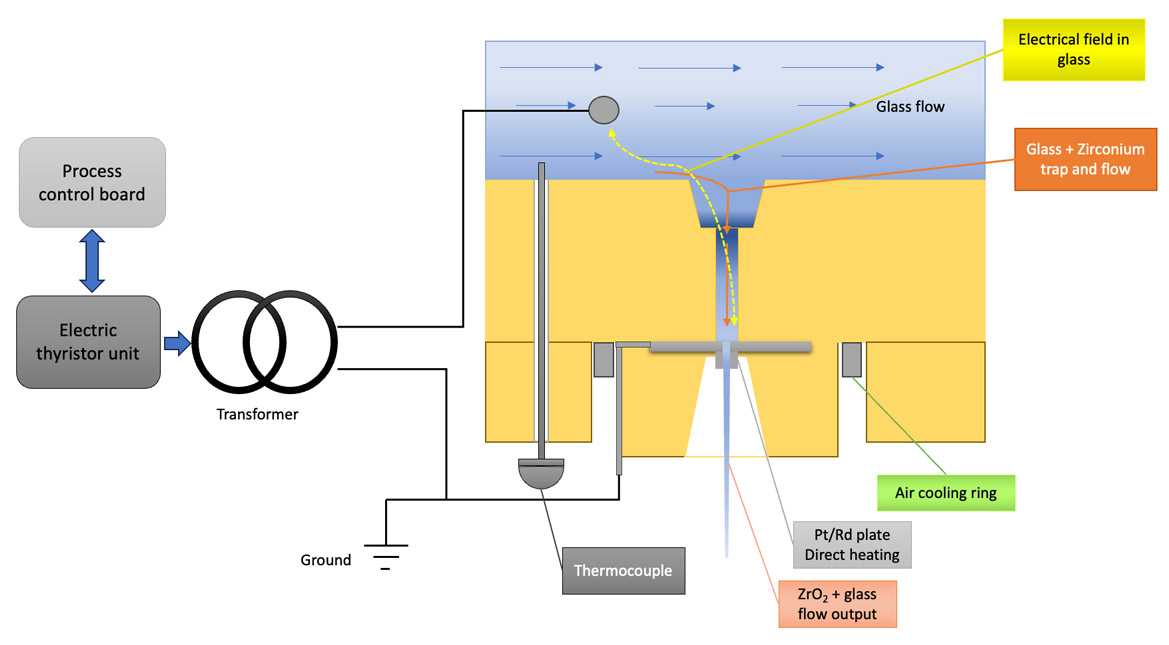
For the Bottom Drain System under normal operating conditions, an electrical power consumption of approximately 2 to 10 kW is typical. The quantity of glass removed depends on various factors, but Glass Service’s experience suggests a drainage rate between 300 and 1500 kg/day is adequate. Typically, the Bottom Drain system operates continuously, although intermittent operation is possible for higher product quality.
Glass drainage is primarily influenced by the outlet nozzle’s size. An electrical heating system maintains a constant temperature at the outlet nozzle, ensuring a consistent glass pull rate. Power adjustment, synchronized with temperature, stabilizes the pull over time, enabling control of the drained glass flow by increasing or decreasing power.
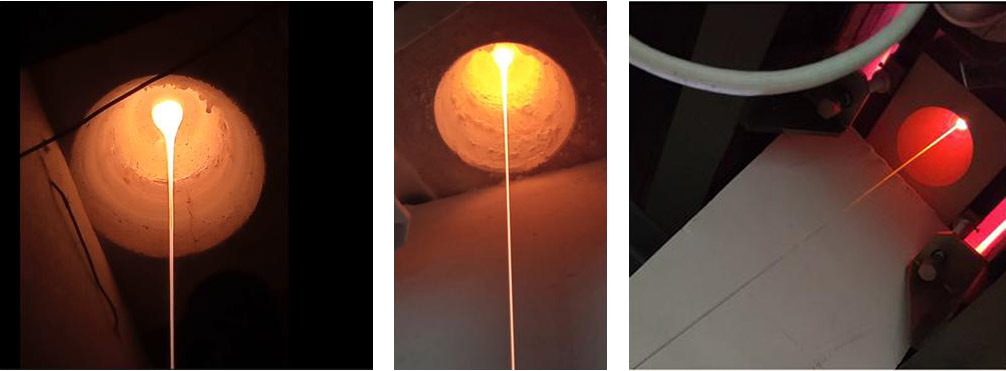
Problem
Bottom Zirconium stream capture
Solution
- Special bottom refractory design with a trap
- Installation of trap in main glass stream, usually distributor or forehearth (not in melting area)
Glass drain flow control
- Electrical heating Pt/Rd plate with high precision regulation thyristor
- Thermocouple in drain area for glass temperature reading
Glass drain flow maximum value
- Correct sizing of plate hole
Water cooling manage
- No water used
- Cooling ring by fans air cooling, dry electrode (air by fans)
Glass voltage residual in glass output drain
- Electrical grounding of output Pt/Rd plate
Long life and stable flow in drain
- Use of Pt/Rd plate and drain hole nozzle
Improved product quality
The Bottom Drain System effectively eliminates visible zircon cord in production, confirmed through chemical analysis of drained glass, specifically ZrO2% content.
This capability ensures enhanced product quality and consistency, addressing a common issue in glass manufacturing.
The image depicts a real-life scenario of a specialized borosilicate glass application, specifically designed to withstand high levels of corrosion on refractories. This bottom drain system is installed within the distributor main stream, showcasing its adaptability and effectiveness in challenging environments.
In red the glass drain out, ZrO2 increase from glass basic 0,1% to 2% , drain flow 40 Kg/h continuous operation.
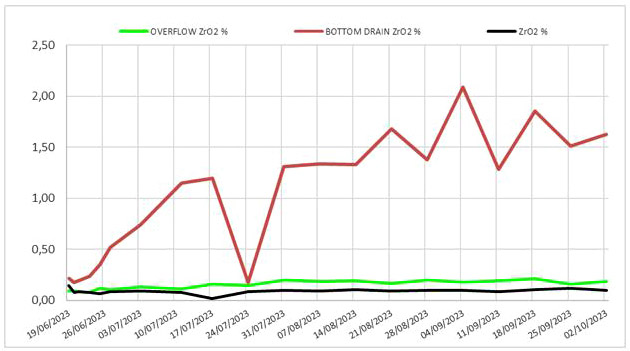