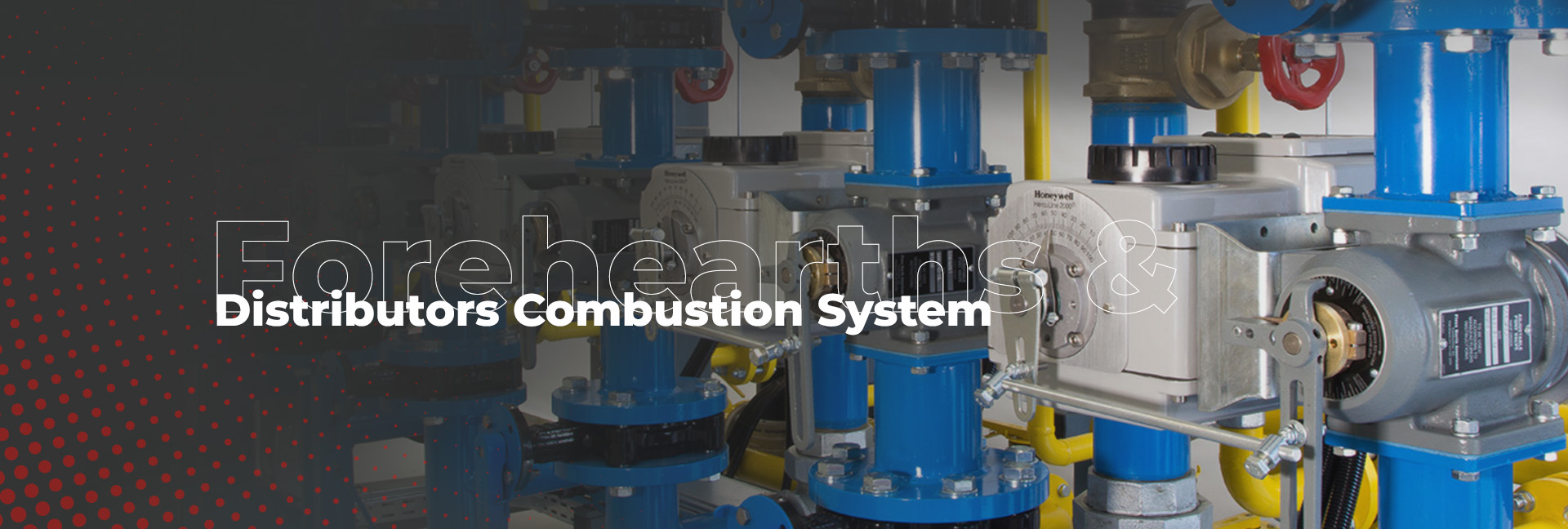
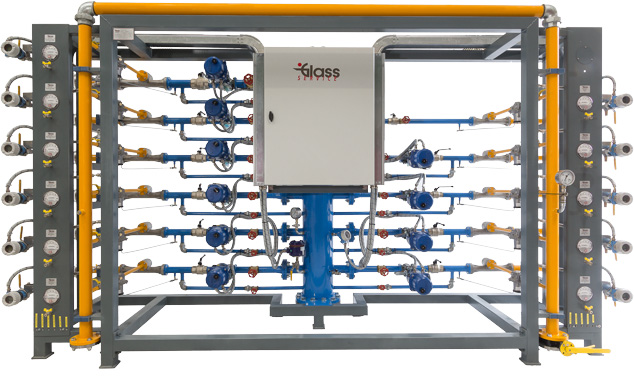

Furnace equipments products
Forehearths & Distributors
Combustion system
An energy efficient forehearth and distributor combustion system is essential for consistent quality production in the glass industry. Good control is essential, particularly in the case of special or coloured glasses (e.g. green, amber) where a stable redox condition in the forehearth superstructure is essential for good quality production.
The forehearth and distributor combustion system developed by Glass Service is the result of 22 years of experience supplying to the glass industry. The system used is the premix gas/air type and can be used with natural gas or LPG.
USEFUL LINKS
DOWNLOAD BROCHURE
The combustion system satisfies the demands of todays glass industry:
GADP Combustion System

Correct combustion ratio in the full range of flow (3 – 50 mbar manifold pressure)

Linear flow valve control characteristic

Stable ratio condition during burner pressure fluctuations

Stable ratio conditions after a burner nozzle change or cleaning

Easy and precise manual setting of the gas/ air ratio for each zone

Wide range of flows and sizes (from DN25 to DN100)

- Special glass
- Table ware
- Colouring forehearth
- High ratio stability even when burners are dirty or blocked
The GADP combustion system is based on the constant ratio between the DP (differential pressure) at the air orifice plate and the gas regulation valve. The GADP is not influenced by burner pressure fluctuations or by dirty or blocked burner nozzles.
The GADP technology is recommended for use in medium and high burner flow applications. In the case of high flows, a butterfly air valve can also be use.
The manifold pressure available using GADP is from 6 to 50 mbar and Glass Service is able to supply burners system for both low and high pressure applications.
Standard Mixer-Zero
Governor (ZGT)
- Linear air valve
- Manual max air valve flow setting
- High loop control stability
- High ratio stable on full operating range
- Pressure tapping upstream the mixer
- Ratio independent control single zone
- Recommended for container industries
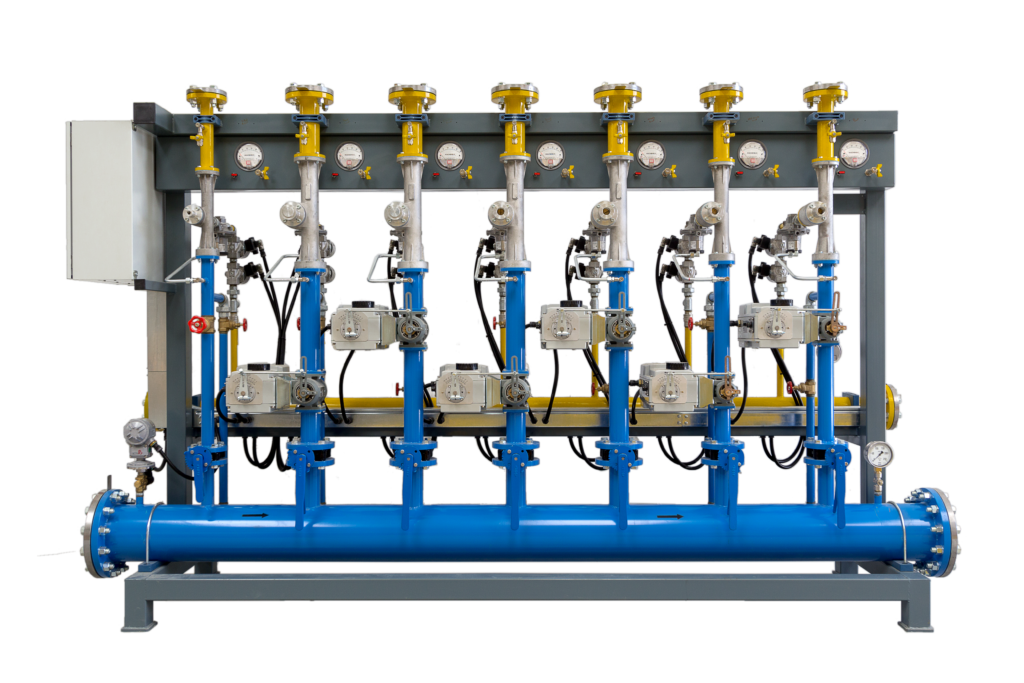
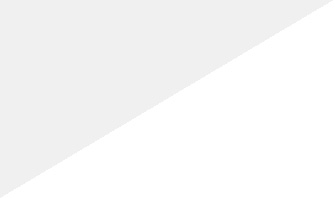
The mixer Venturi and zero governor has been the common standard in the glass industry for many years and is used in all glass types including tableware, containers and special glasses. That system is based on the constant gas/ air ratio at the burner. Glass Service has developed a new ZGT combustion system based on the traditional system but with a number of changes technically that improve the quality and performance of the combustion system. The Glass Service solution increase the system performance and the stability of the gas/air ratio.
Glass Service use a specially designed air valve that can be adjusted to give the required maximum flow using a manually adjusted curtain. The max air flow can be set zone by zone during installation to set the servomotor valve to the max value (100% opening). The full stroke of the servomotor and valve increases the loop control stability.
The zero governor pressure tapping upstream of the Venturi mixer increases the gas/air ratio range and reduces the risk of gas leakage should the zero governor be damaged. The pressure range using ZGT is from 3 to 50 mbar and Glass Service is able to supply both low and high pressure burner systems. Because of the stability across the full range and in particular at low pressure and low flow, this system is highly recommended for use in the container industry.
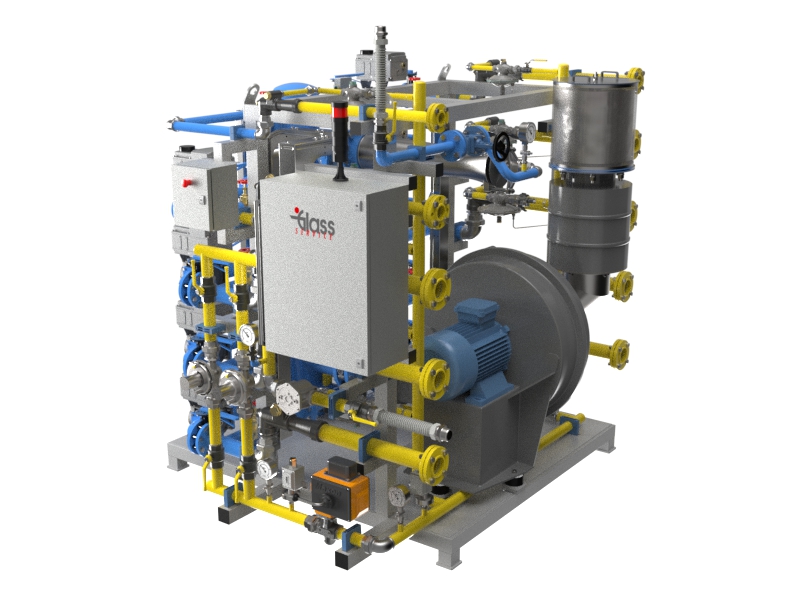
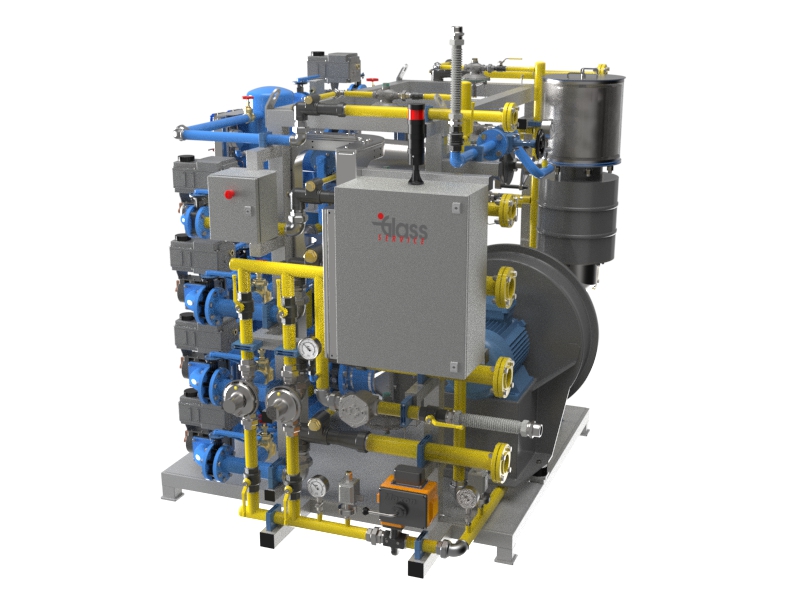
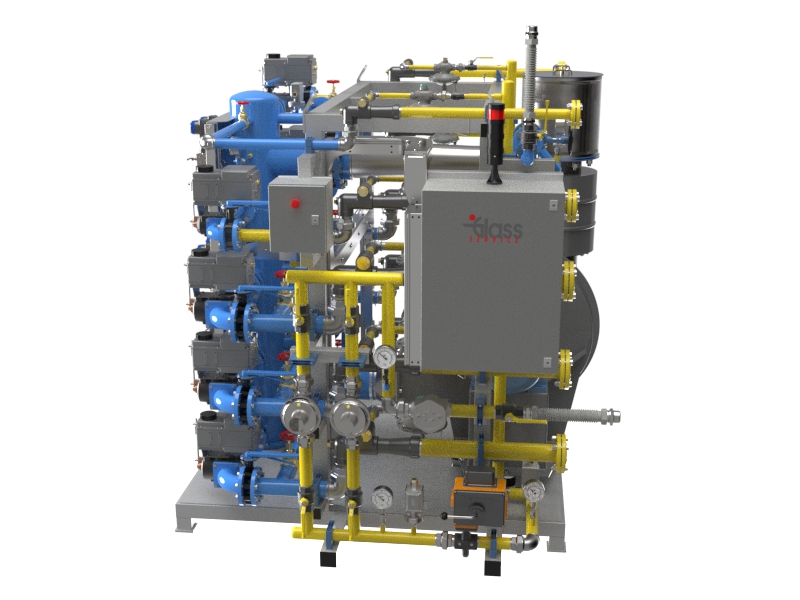
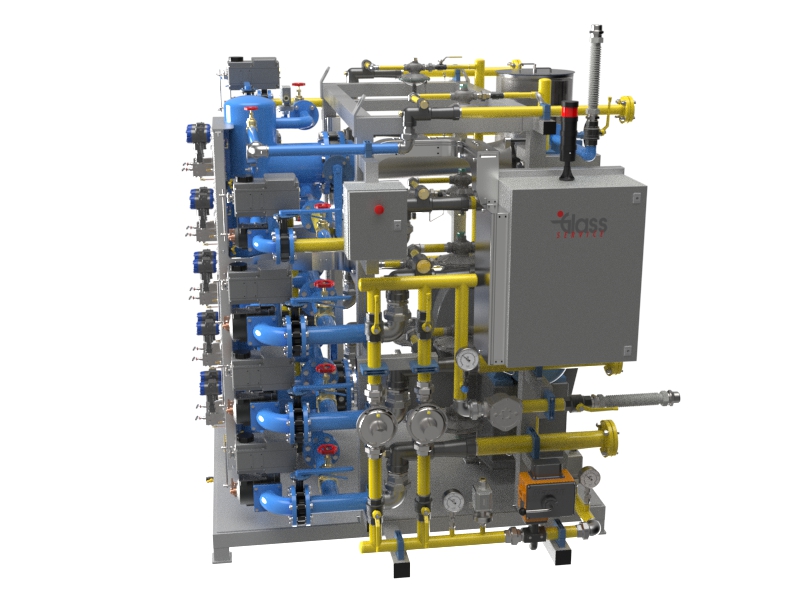
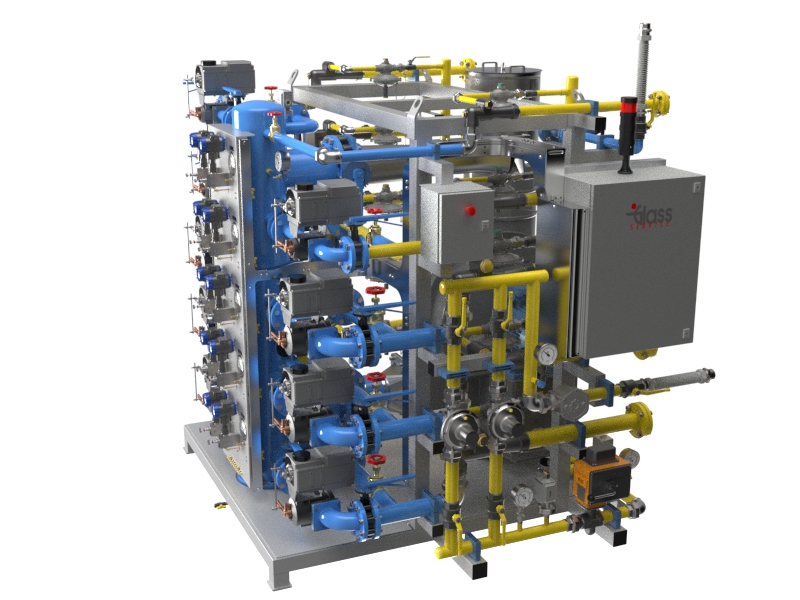
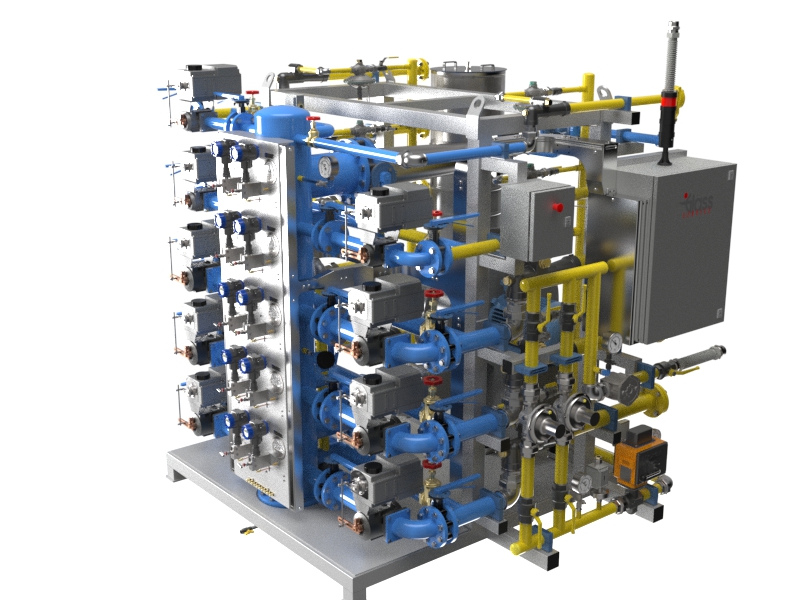
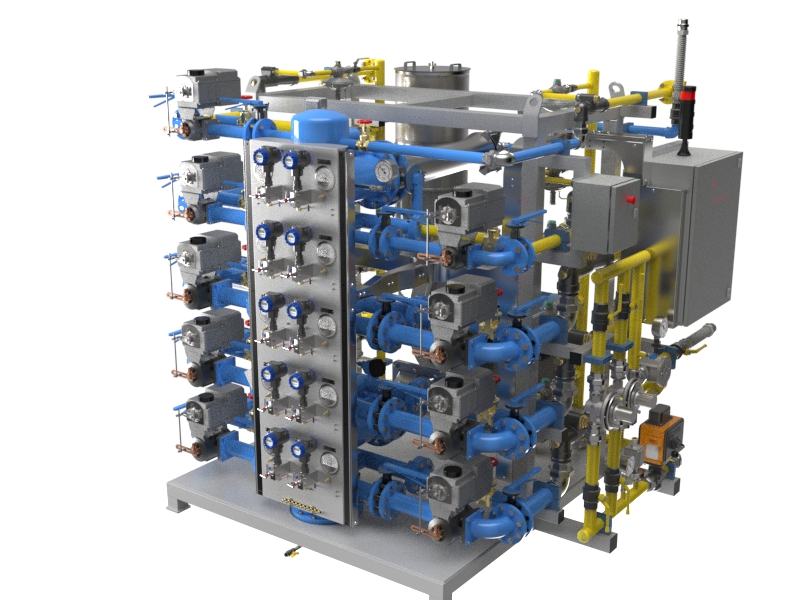
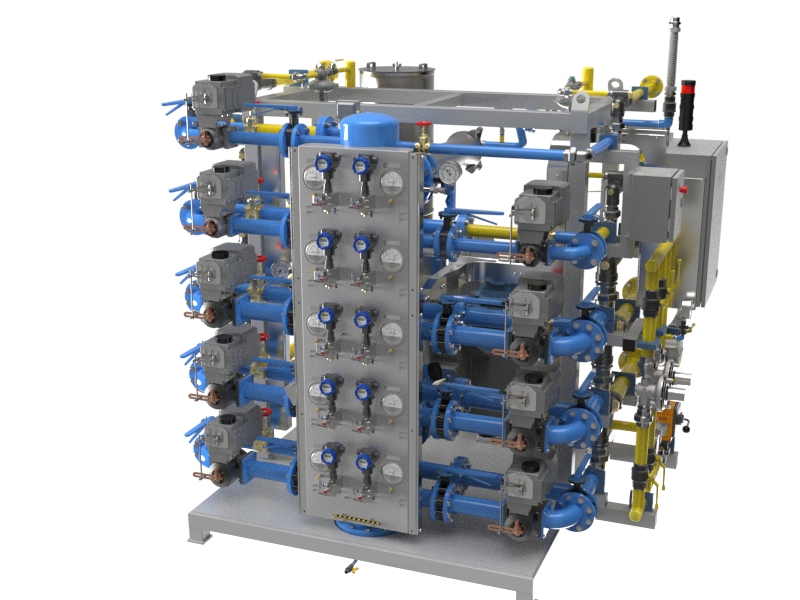
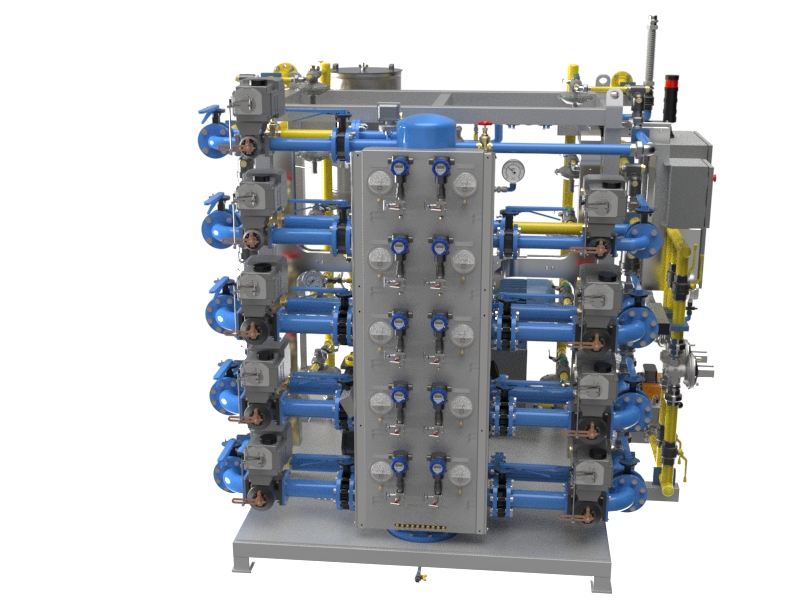
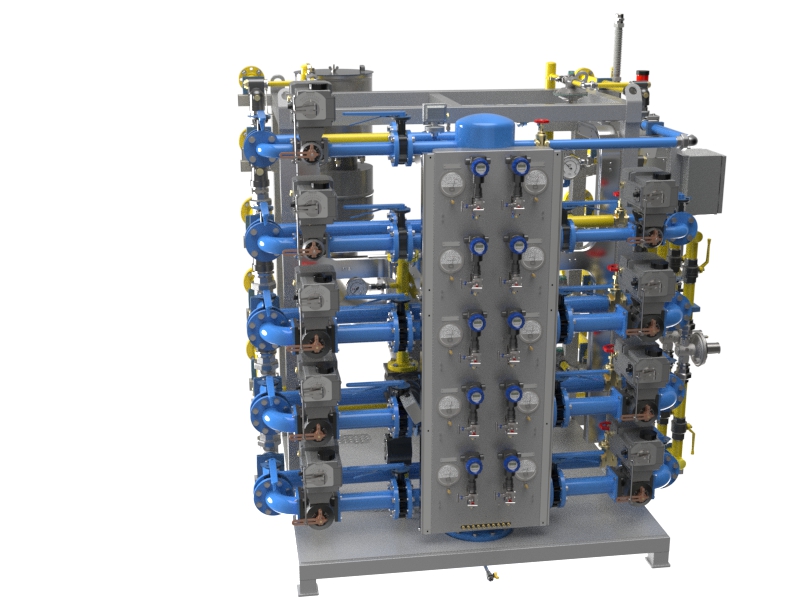
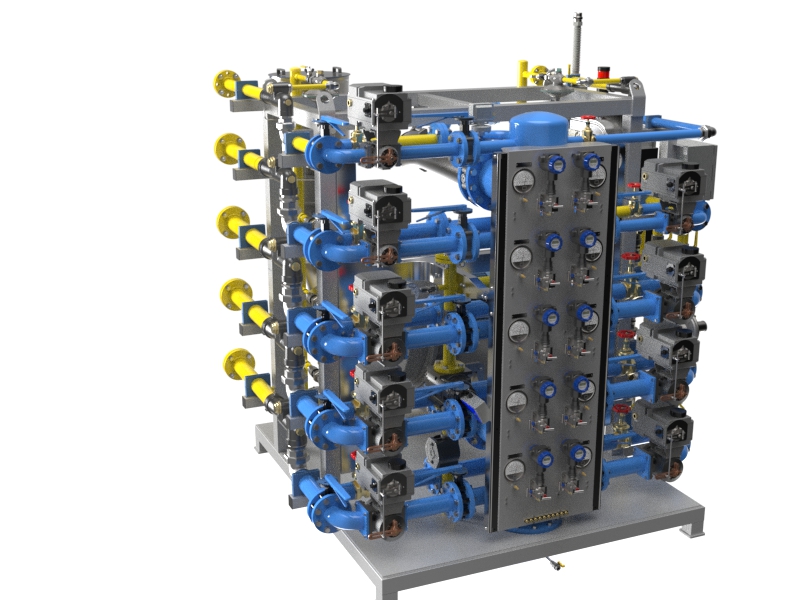
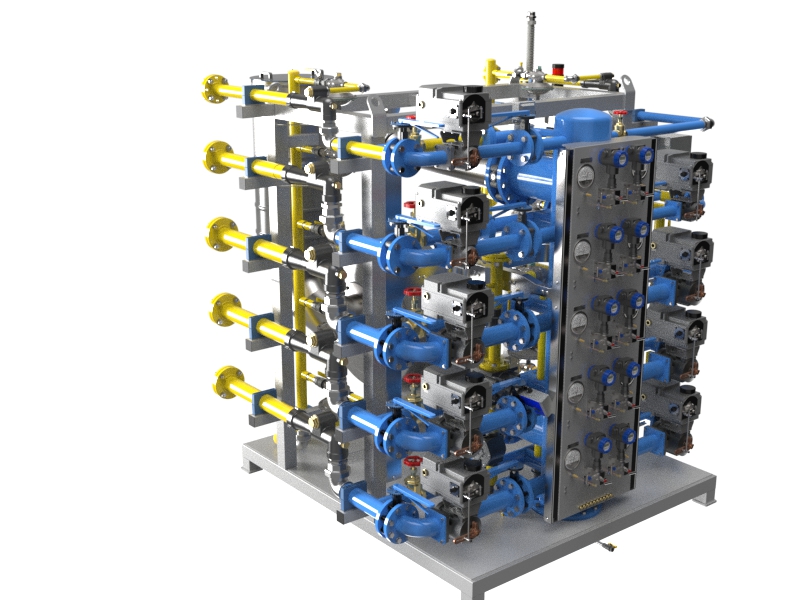
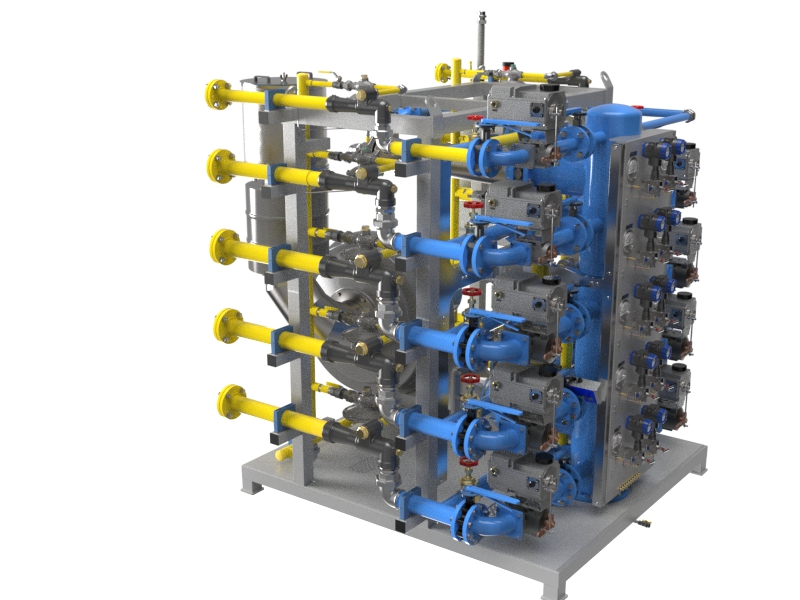
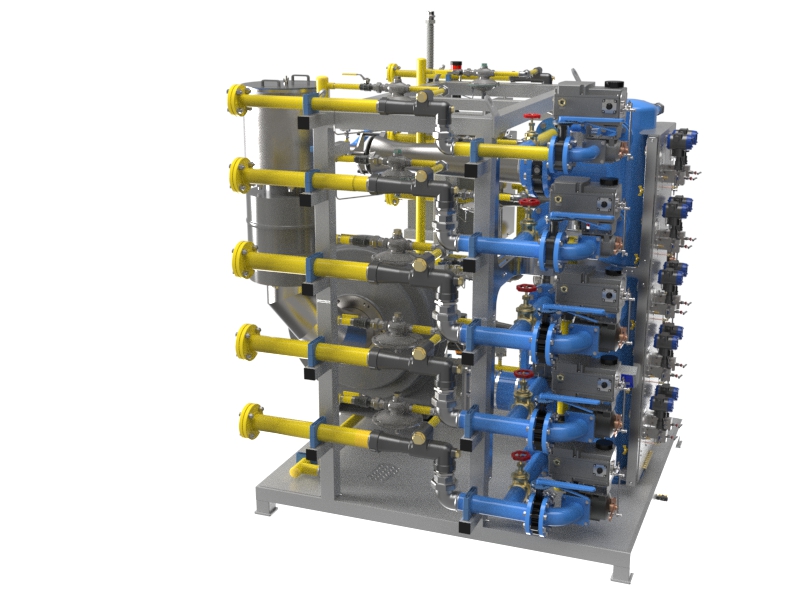
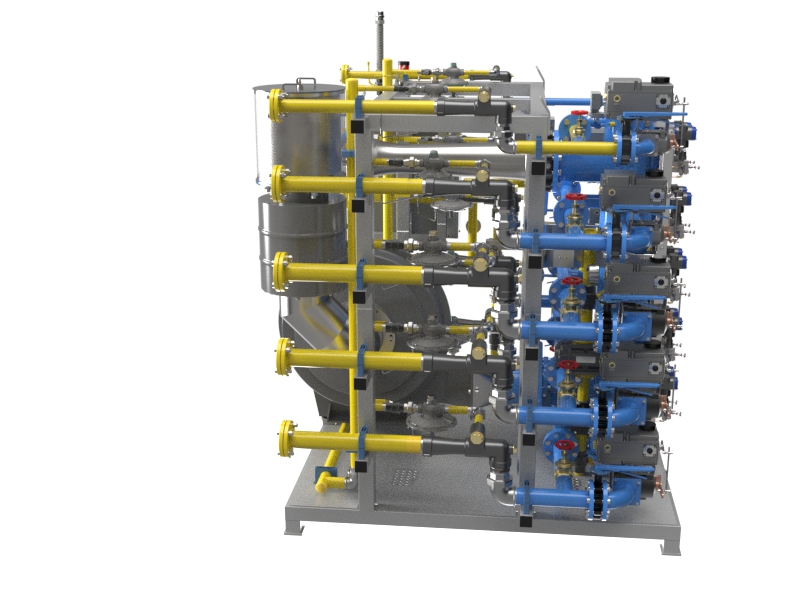
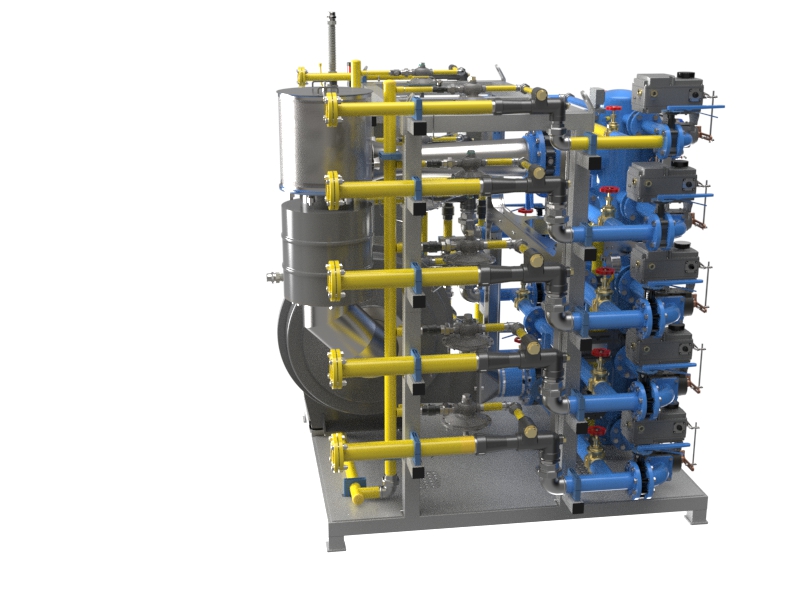
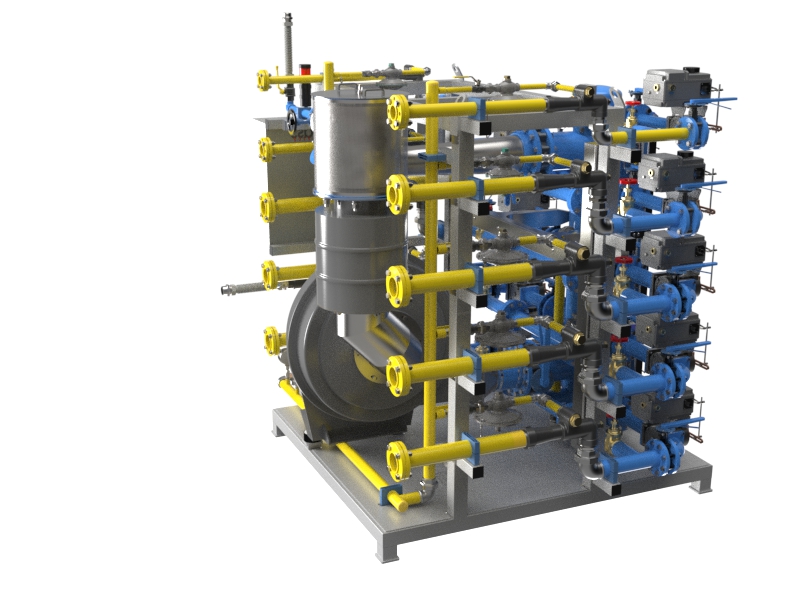
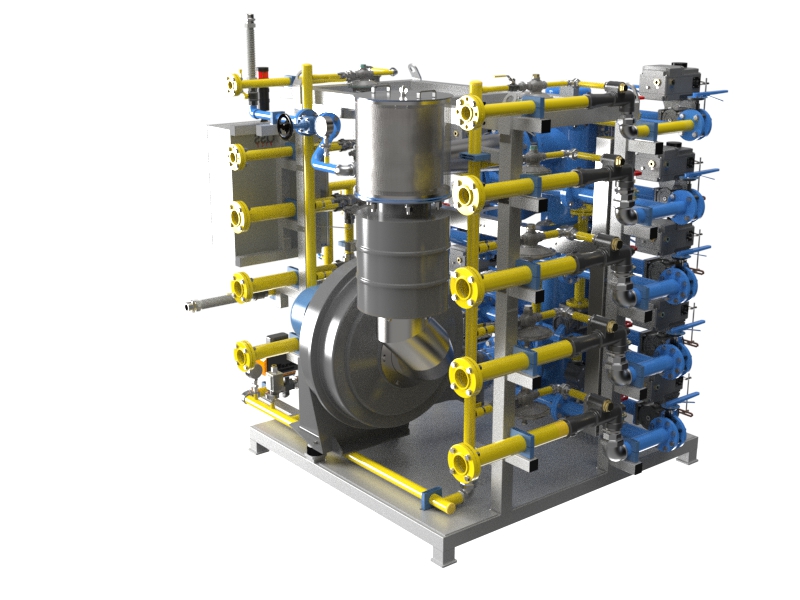
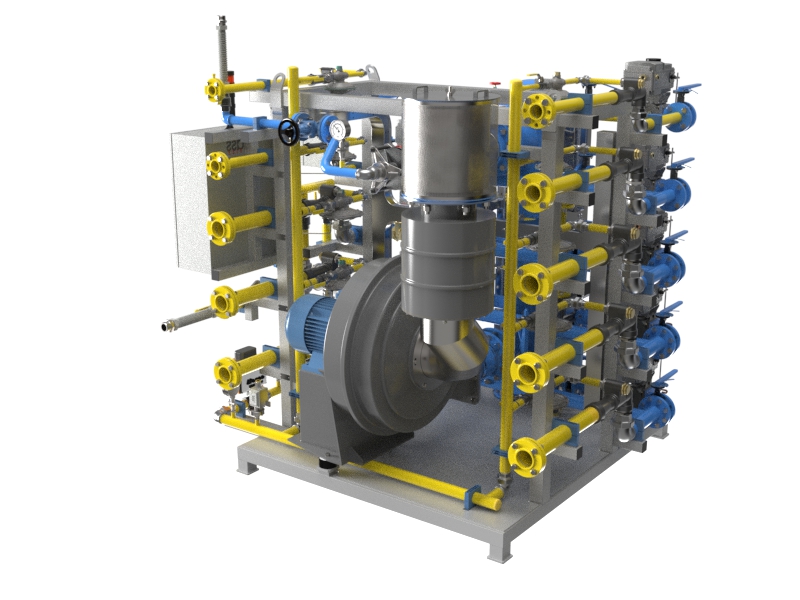
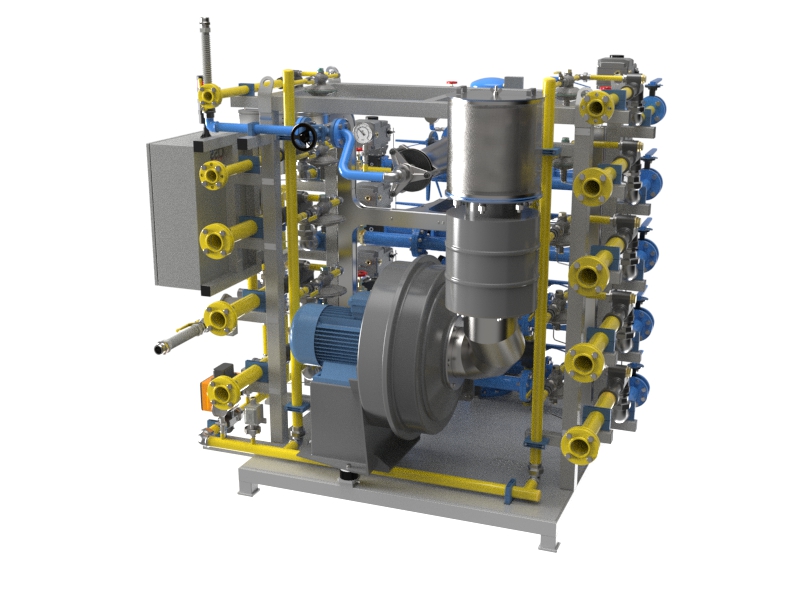
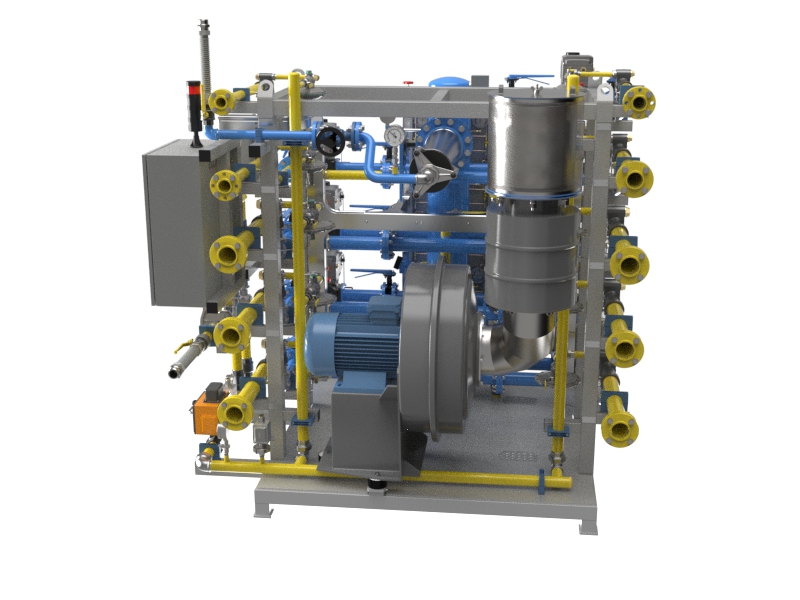
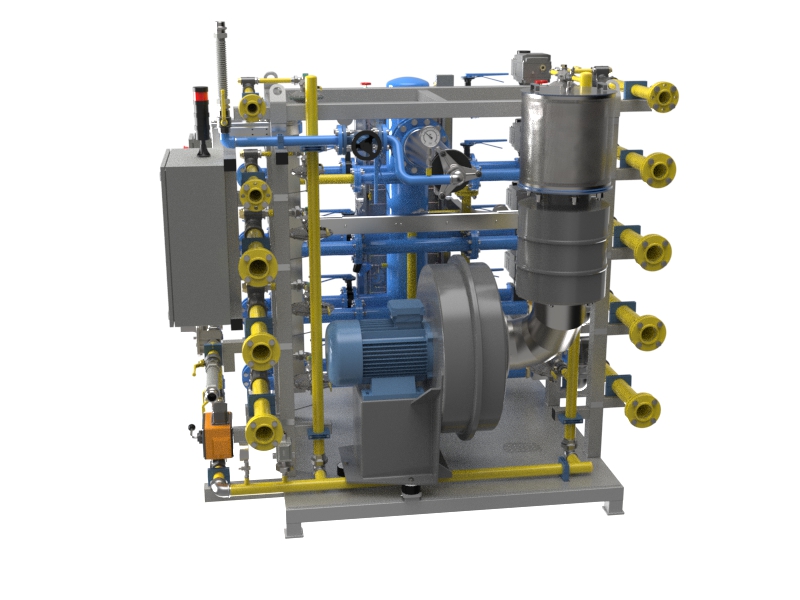
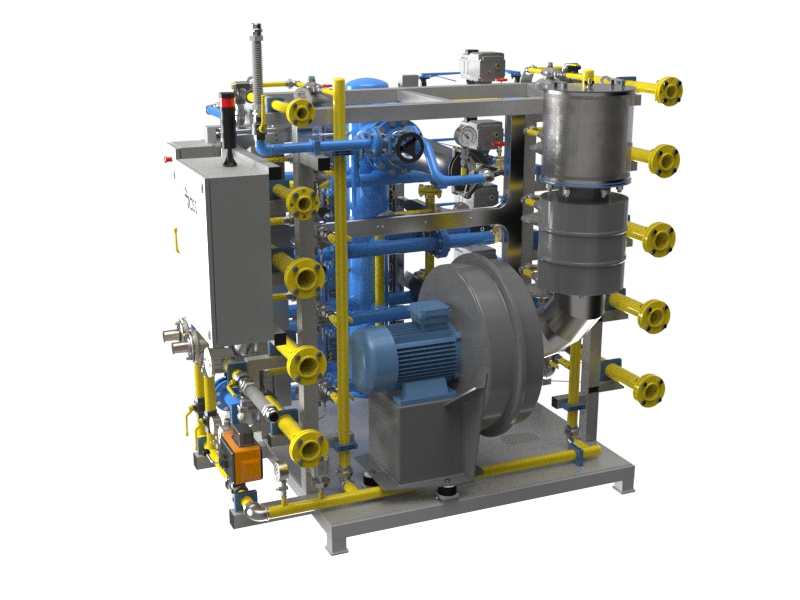
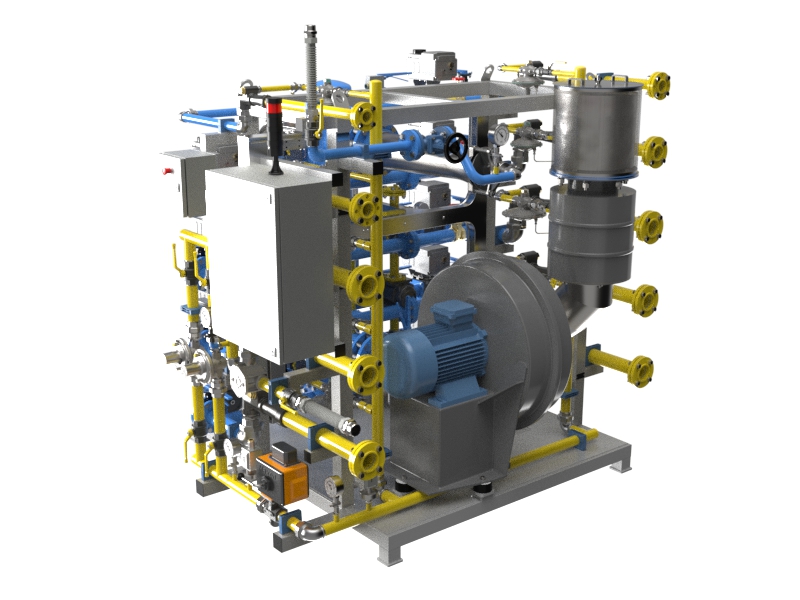
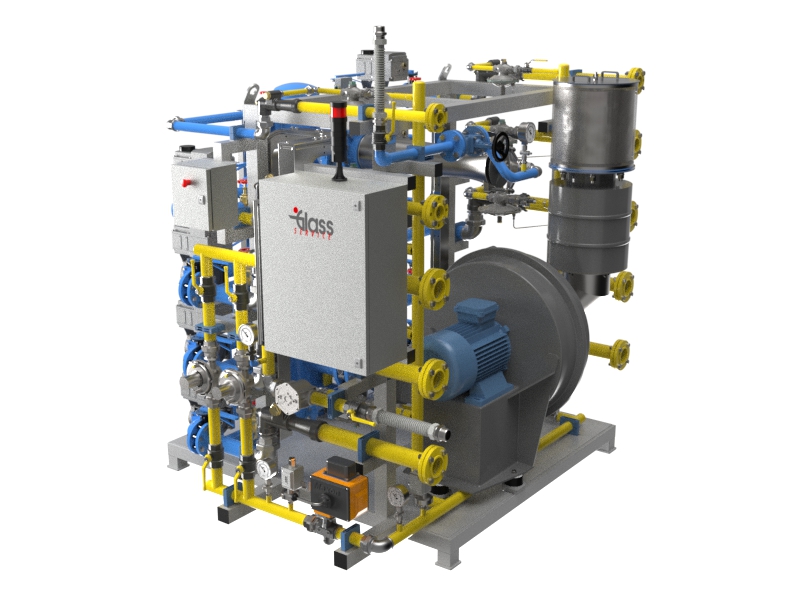
OMN Combustion System
- High ratio stability on full range
- High ratio stability in time
- Recommend for high performance Forehearths in container industries
-
Recommend for high performance Forehearths in container industries
(green and amber) - Air orifice and gas needie size tailor made on specific combustustion zone flow
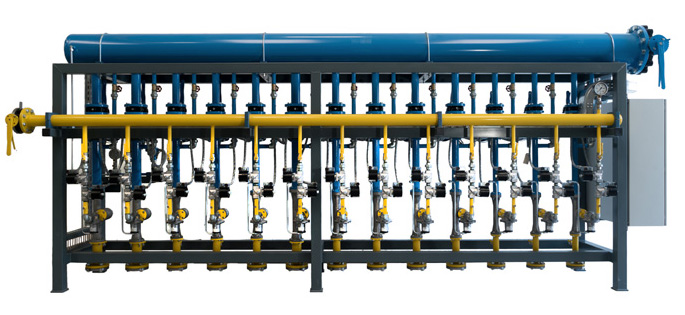
Glass Service introduce a new concept of combustion system utilising the new OMN device. The system uses a new concept of combustion ratio control. It comprises an air orifice plate and a double stage zero governor. The pressure tapping for the zero governor is taken upstream of the orifice plate flange chamber. In this chamber there is an over pressure which causes a flow restriction.
The gas input is in the orifice plate chamber downstream of the orifice plate and is regulated by a high precision gas needle valve. The size of orifice plate and needle valve are designed specifically for each combustion zone. Another new innovation is the use of a double stage zero governor. This increases the ratio stability in the full range and in real time.
- High ratio stability over the full operating range
- The ratio is stable and no adjustments are required
- The pressure tapping is upstream of the mixer
- Independent ratio control for each zone
- Ability to operate over a wide range of ratios
- High precision gas regulating needle valve
- Each air orifice plate and gas needle valve designed for each specific combustion zone to give improved fuel efficiency
The pressure range available using OMN is from 3 to 50 mbar and Glass Service is able to supply low and high pressure burner systems.
Because of the stability across the full range and in particular at low pressure and low flow, this system is highly recommended for use in the container industry.
The OMN system ensures the best performance of gas/air ratio stability over the full range of flows without the need for adjustment over time.
Construction Details
The forehearth & distributor combustion skid deigned by Glass Service are compact and easy to install. The combustion system is preassembled on the skid ready for installation, complete with all up to date equipment necessary for the best performance. For each zone the required technology is installed (ZGT; GADP; OMN). Other equipment are also installed for best performance.
- Pressure indicator for each zone
- Pressure transmitter for each zone
- Explosion relief valve for each zone
- Gas flow meter for each FH or Distributor
- Mix test analysis connection for each zone
- Air pressure switch
- Gas pressure switch
- Skid cabling and local junction box
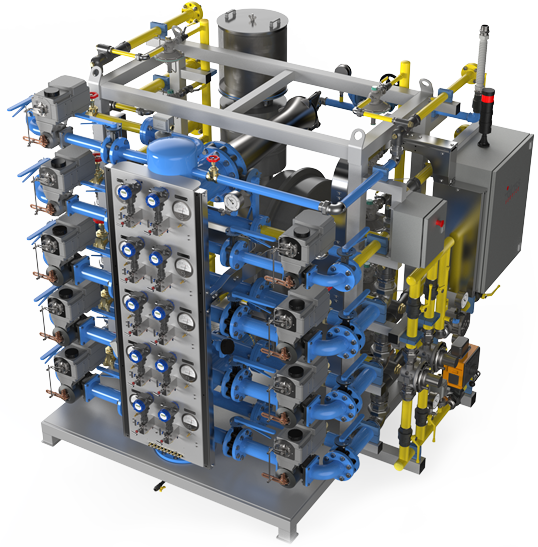
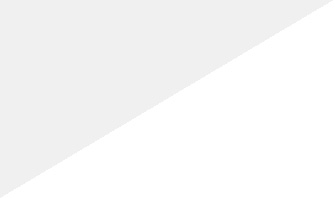
Burners & Manifold
Glass Service developed the foreheart and distributor burner technology along with the necessary manifolds and mountings for the forehearth casing. The burners are totally sealed to the refractories. The burner nozzle are available in several sizes as standard production, with different nozzle diameter available on request.

1/4 inches / 6,3 mm

3/8 inches / 9,5 mm

9/32 inches / 7,1 mm

5/16 inches / 7,9 mm
The burners are manufactured in special high temperature resistant steel. The burners are supplied complete with manifolds and he brackets that allow 3 directional
movement for better installation and adjustment after heat-up. Each manifold is supplied with long flexible connection and manual shut off valve for burner maintenance.