How tubular glass manufacturing processes can affect the final product stability and technological improvement to mitigate it.
Al – Epinephrine interaction: a related example.
Al2O3 is one of the primary constituents of Type I glass, commonly used in pharmaceutical glass container manufacturing. The presence of Al2O3 in the glass formulation has a double impact: as a glass network former (together with SiO2 is a part of “refractory constituents”) and as a network stabilizer giving to Al2O3 containing glass a higher chemical resistance lowering the alkaline release.
Clearly Al2O3 is a necessary constituent in Alumino-Borosilicate glass, and as Biavati et al.(1) showed, Type I glass may produce a sensible release of Al ions in specific conditions. This tendency can subsequently produce a variety of chemical interactions between released Al3+ and constituents of drugs contained therein, that can evolve into a complete API degeneration catalyzed by the amphoteric nature of Aluminum Ions, depending on the solution pH.
One interesting API is the Epinephrine / Adrenaline commonly used in combination with Lidocaine in dental anesthetics. Studies on factors that could affect the degradation of Epinephrine stored in glass containers do not give relevant results regarding the role of Al (III) released from the inner surface of glass containers(2)(3), but periodical checks of control samples in storage showed that Epinephrine effects had been strongly reduced after only a few months, with as little as 0,5 ppm of Al in the solution: the result is a marked reduction of anesthetic shelf life (around 1/3) linked to high costs and loss of market appeal.
There are factors that can mitigate glass chemical release and Al as well, such as a correct forming/converting process of the glass and the washing of the container before filling.
As far as Al release from converted tubular glass containers is concerned, it has been found that one of the crucial parameters not usually considered, is the tubular glass manufacturing process and consequently, the materials the molten glass came in contact with.
In the Danner process, the tubing form is obtained rolling a glass flow on a rotating sleeve generally made of refractory materials such as ones with a high Zirconia and/or high Alumina content.
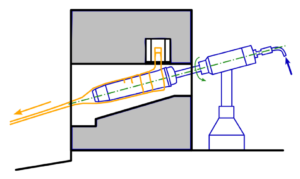
The more advanced technologies improved the production process in terms of glass quality by using a surface coated sleeve (metalized with Noble metals). Comparing different tubular glass containers obtained in different ways, a model based on Thin film Theory has been hypothesized and then confirmed by experimental data, to explain differences in terms of Al release between coated and uncoated refractory sleeves used.
In particular, the experimental data collected showed that during glass tubing production, it is reasonable to presume a thin film formation at the interface between the molten glass that flows over and the refractory sleeve that is rotating underneath (SEM analysis of glass/sleeve interface and EDS analysis of refractory section at various distance from interface shown a distance based Al concentration gradient).
This thin film is constituted by a Na and Al enriched glass. Na moving from the glass where is the more mobile ion which occupy the glass network free spaces, Al moving from sleeve surface. The driving force, in both cases, is associated with a concentration gradient (Fick Law)
Considering the common Type I glass and refractories composition (Al2O3 content is around 5-7 %in the glass and up to 60% in High Al content refractories), it appears clear how the Al migration could create a time based porosity of the sleeve surface that increases the aggression rate. The Alumina, migrated from refractory to the glass, tends to occupy the free space present in the structure (considering the relative low viscosity of the glass at the forming point ≈10 4 poise), instead of linking with an existing network(4). The result is the formation of a thin glass film enriched in very mobile Na and Al that slide on the sleeve, that concur to create the inner surface of glass tubing and consequently of the glass container in contact with the contained solution.
Glass tubing produced this way shows a higher Na release and, in time, Al release.
The implementation of a metal (noble) coated sleeve technology, is effective not only in terms of Na release (strongly demonstrated by experience) but also concerning Al release, avoiding the formation of the above mentioned contact between glass and refractory and the Al migration at interface.
Comparison tests, made on tubing glass containers obtained with coated sleeves, showed a reduction close to 90%, in terms of Al release.
By the abovementioned consideration, it is reasonable to expect that the Glass Tubing production technology commonly known as “Vello”, based on static metallic (metalized) sleeve (no refractory/glass interface at the inner tube surface formation), can give the best performance in terms of Al release and containers obtained from above mentioned tubes could guarantee a long term stability of contained Epinephrine.
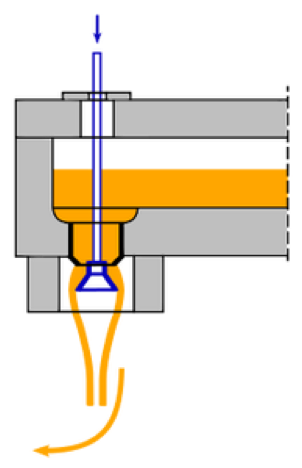
- Alberto Biavati; Paolo Amadei – “Significance of Aluminium Release from Type I Borosilicate Glass Containers” – Pharmind 2010.pdf
- David Stepensky; Michael Chorny; Ziad Dabour; Ilana Schumacher – “Long-term Stability Study of L-Adrenaline Injections: Kinetics of Sulphonation and Racemization Pathways of Drugs Degradation.pdf”
- O’Conceanainn M; Hines MJ – “The kinetics and mechanism of the reactions of aluminium (III) with gallic acid, gallic acid methyl ester and adrenaline” – J Inorg Biochem, 2001 Mar; 84 (1-2) : 1-12
- Balconi“Esperienze di attacco sui silicati di alluminio” – Rend. Soc. Min. It. – vol.1, pag. 236